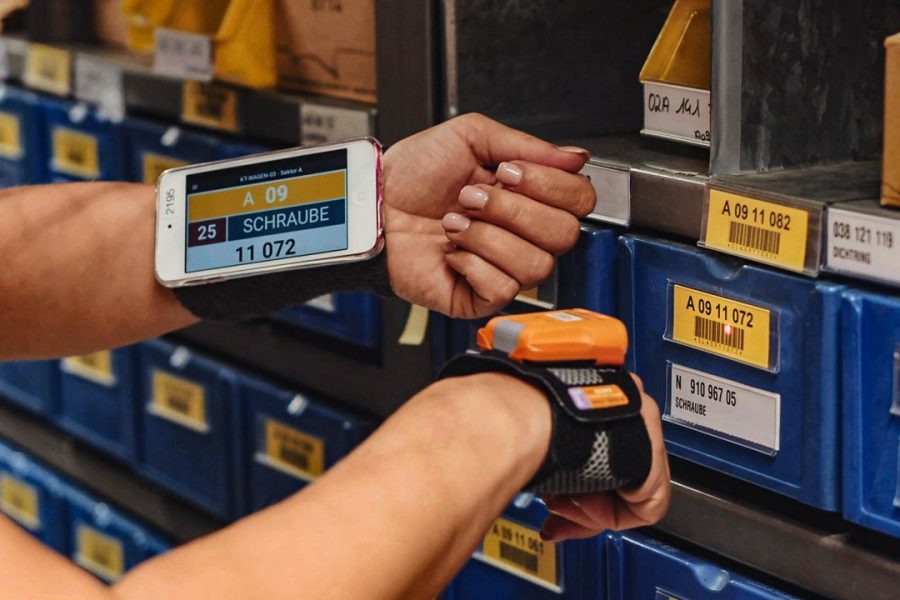
Porsche Teilevertriebszentrum (TVZ) in Wals is the hub for supplying service companies with spare parts for the VW, Audi, Seat, ŠKODA and Porsche brands in 18 countries. Our spare parts logistics system ETN forms the top link in this supply chain and supports the entire spare parts process from the TVZ itself to the service companies or importers in our partner countries.
In January 2019, the TVZ launched an extensive digitization project in close collaboration with the ETN team. Taking its cue from the Industry 4.0 and Logistics 4.0 technology trends, the project was named “TVZ 4.0”. The project involved rethinking the delivery process for spare parts from the customer’s initial order through to the ready-packed part.
From “Push” to “Pull”
Analyses of the existing process highlighted several weak points; including long lead times, sorting costs and even errors in the process. In the course of the TVZ 4.0 project, the team subjected this process to a complete redesign. A “push” process, in which a central command centre controlled the warehouse staff, gave way to a “pull” process in which the colleagues in the warehouse can call up their working positions for themselves.
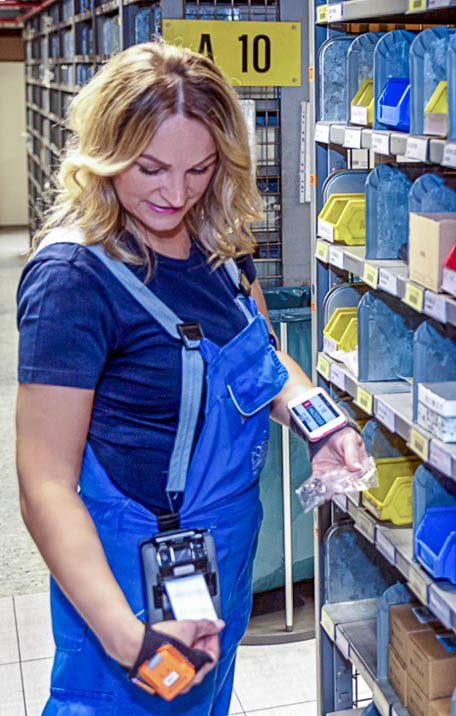
Newly kitted-out with a scanning glove, label printer and portable terminal
As part of the newly digitized process, all 150 employees in the warehouse are being equipped with mobile devices:
- a scanning glove – so that both hands can be kept free;
- a mobile label printer for printing labels wherever the employee is at the time;
- a portable device (iPod Touch or iPad).
Complex logic, simple interface
Via the display, employees are directed to the correct storage location just as if they were using a navigation device. There, they scan the storage location with the scanning glove and the mobile label printer immediately prints out the correct label. The user interface is limited to the absolutely necessary information: which item is to be retrieved from where and in what quantity. Only when problems arise, such as a damaged part, is a detailed view displayed.
The most complex issue to become apparent in the course of the redesign was how to optimise the employees’ work paths. In the new process, the ETN uses a complex logical process to ensure that all the important parameters are taken into account within fractions of a second:
- the shortest route along which as many items as possible can be picked up;
- the urgency – here, among other things, the departure times of the forwarding trucks need to be taken into account;
- the uniform utilisation of subsequent storage areas, such as packaging or sorting;
- colleagues’ picking routes, to ensure that no one takes items away from another.
Unlike in the old process, the ETN now also controls the internal container transport system. This allows the system to intervene in a wide range of processes, such as diverting containers when packing stands are combined on late shifts.
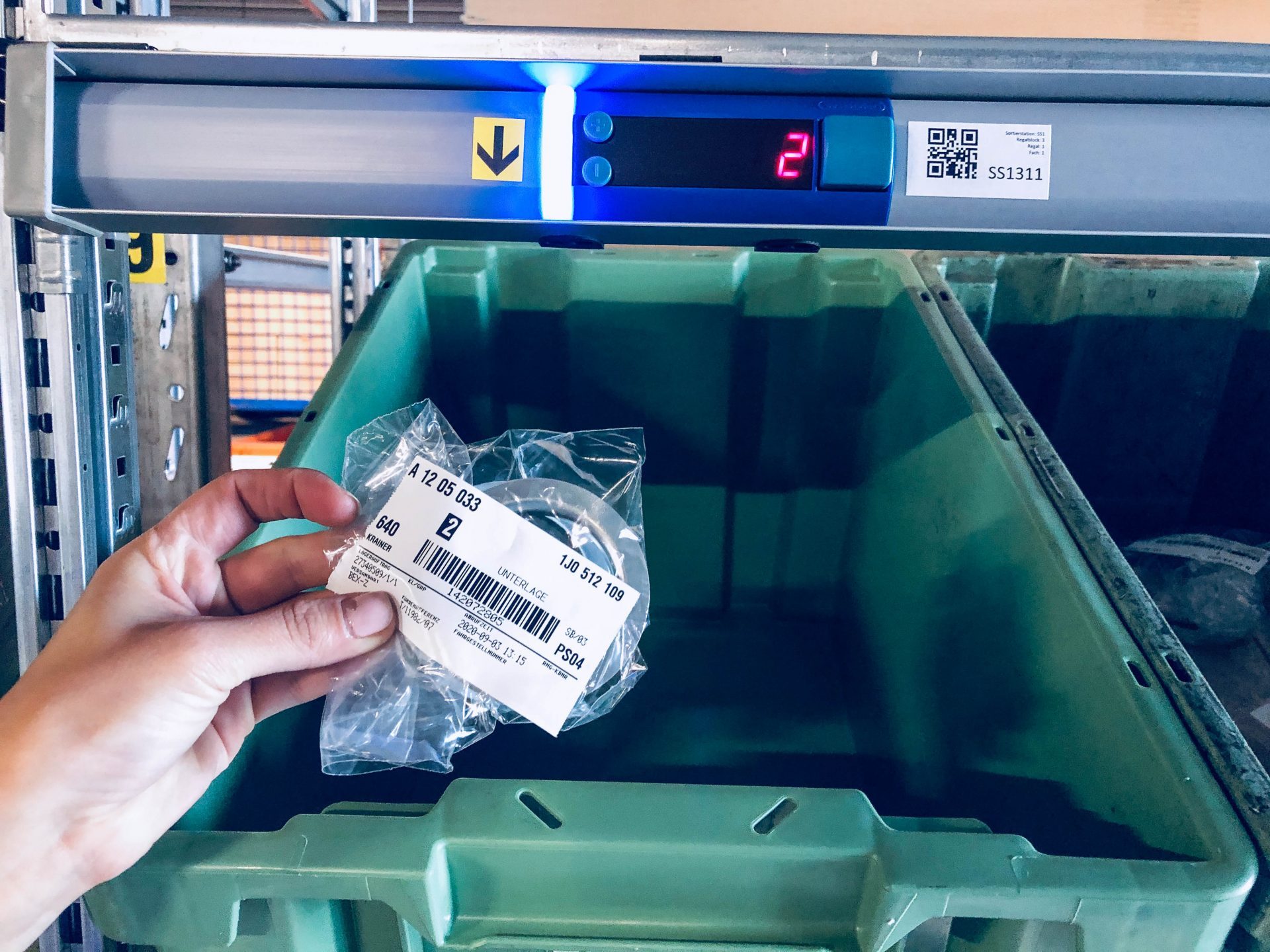
Light guidance prevents incorrect insertions
Process optimisation at all levels
At the sorting station, the employees are directed quickly and error-free to the correct container via a “put-to-light system” whereby a sensor grid prevents false insertions. Light guidance is also put to use at the packaging station, where they enable further significant optimisation of the process.
By continuously tracking all processes, the TVZ team can now identify potential problems at an early stage and react to them swiftly. This transparency and abundance of data will open the doors to big data and machine learning and allow further optimisation in the future.
Comprehensive change management
The biggest challenge the project team faced was enabling integration during ongoing operations. The TVZ never gets a day off, so comprehensive change management was vital. The new process signifies a radical change to the way work is undertaken. Therefore, it was extremely important to involve the employees from the very outset in the development of the new processes.
The TVZ 4.0 project has been in its pilot phase since this summer, and the new processes are already being thoroughly tested in parallel with the existing procedures. Feedback from the employees has generally been very positive, and suggestions for fine tuning, improvement of ergonomics and software adjustments are gradually being incorporated into the process.
In June of this year, the project was awarded the Change Award by Porsche Informatik in the “Innovation” category. Very well deserved, as we see things – we warmly congratulate the whole team!
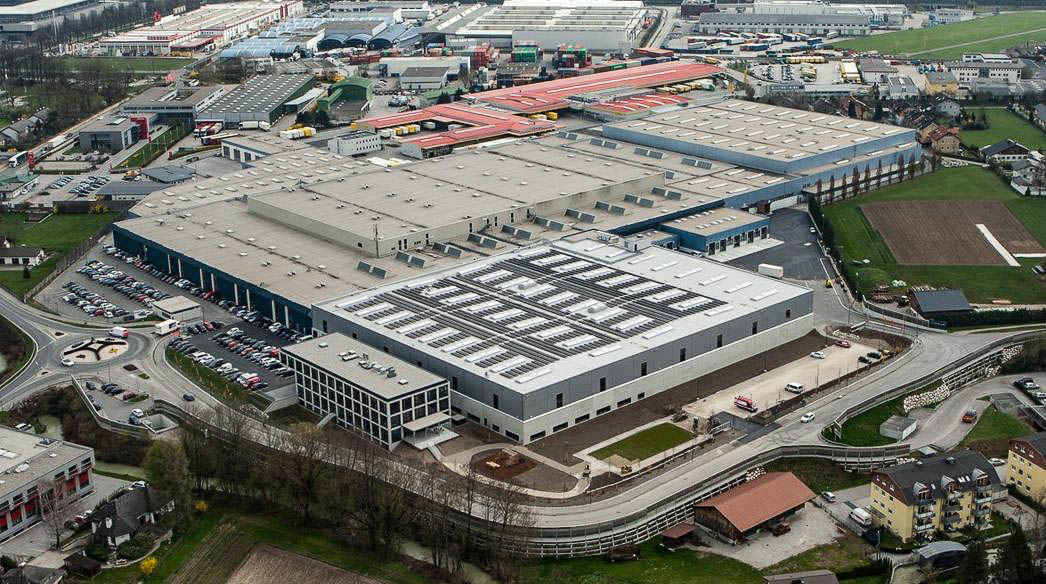
The Parts Distribution Centre (TVZ) is a non-stop operation